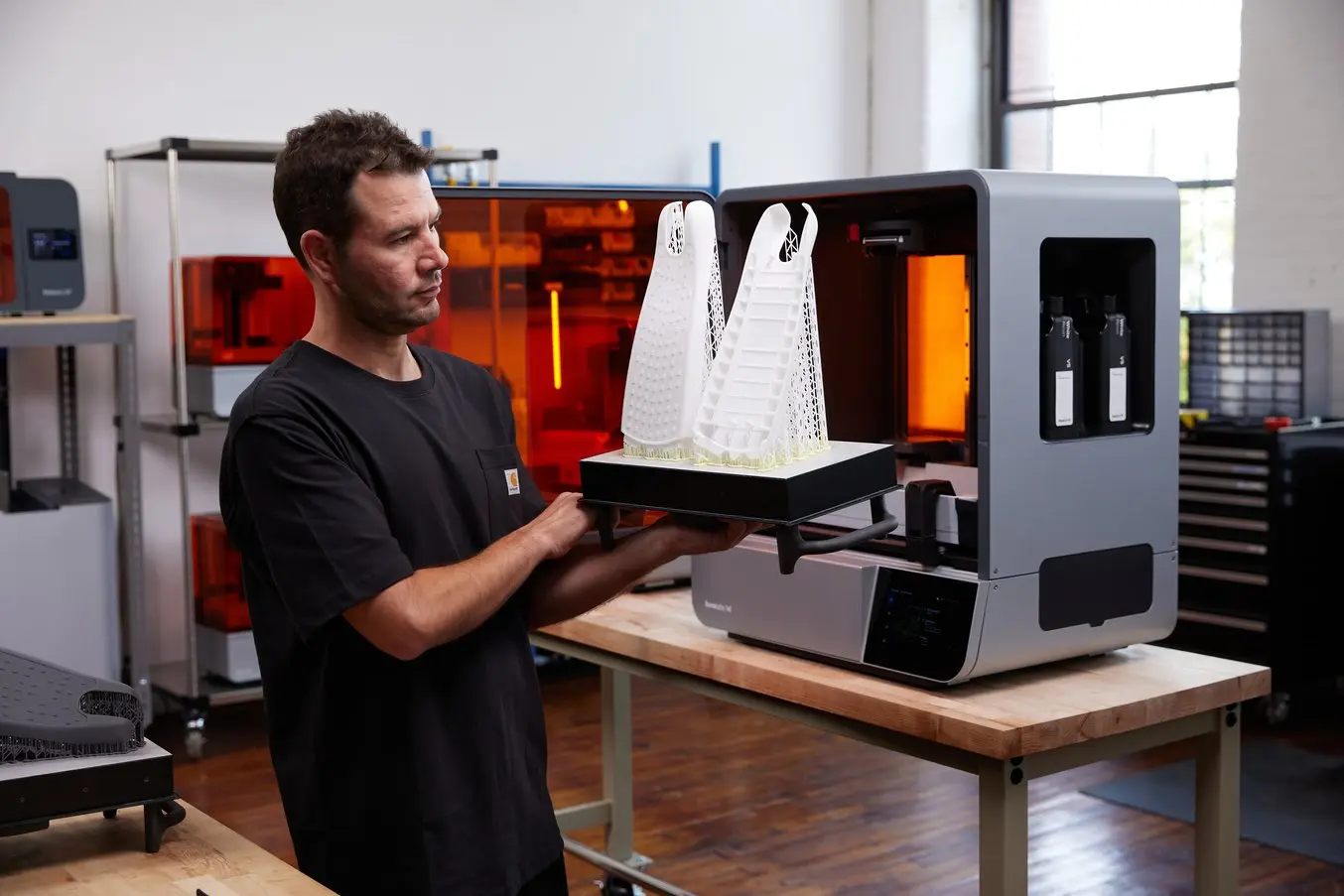
Resin 3D printing is one of the leading adapted 3D Printing technologies in recent years for producing highly detailed 3D parts. The technology is useful for rapid prototyping, rapid tooling, manufacturing aids and even end-use parts due to high accuracy, fast printing speed, different materials in the market and isotropic mechanical properties. The hardware, software and materials innovations of the Resin 3D printer manufacturers led to a spate of processes in Resin 3D printing.
For many years, two classes of Resin 3D printers were broadly defined: stereolithography (SLA) and digital laser processing (DLP). Only a few years ago, some subdivisions of these technologies were introduced and defined further, namely LCD and masked stereolithography (MSLA) 3D printing.
Stereolithography (SLA) and Masked Stereolithography (MSLA) are two of the most prominent resin-based 3D printing technologies. Both rely on photopolymerization to cure liquid resin into solid objects, but they differ significantly in their methods of light delivery, speed, precision, and applications. Here’s a detailed exploration of these technologies to help you understand their strengths and use cases.
What is SLA 3D Printing?
Traditional SLA printers were built around large vats filled with liquid resin where the top layer was selectively cured by the laser positioned above the tank. These systems were large, prohibitively expensive, and required complex infrastructure, limiting their use to the likes of Fortune 500 companies
Formlabs introduced inverted stereolithography 3D printing in 2011 with the Form 1. With the inverted SLA process, a light source (a laser in Form 1) cures the cross-section of the part through a transparent-bottomed resin tank, meaning only a thin layer of resin needs to be dispensed and available for curing at any time. This technology makes it possible to fabricate resin parts using a much smaller printer that fits on a desktop.
SLA 3D Printing Technology: The video is taken from Formlabs
What is MSLA 3D Printing (or LCD 3D Printing)?
Masked stereolithography (MSLA) 3D printing technology refers to any photopolymerization process where a light source is selectively covered, or masked.
It is often used interchangeably with LCD 3D printing, because MSLA printers generally use LCD screens to mask the light and cure only the desired cross-section of the part. However, MSLA can refer to other technologies as well because it means masked Resin 3D printing, regardless of the type of light source or masking technique.
The use of LCD screens in Resin 3D printing came after the development of laser-powered SLA and DLP 3D printing, enabled by the rapid development of display technologies due to their prevalence in other types of electronics.
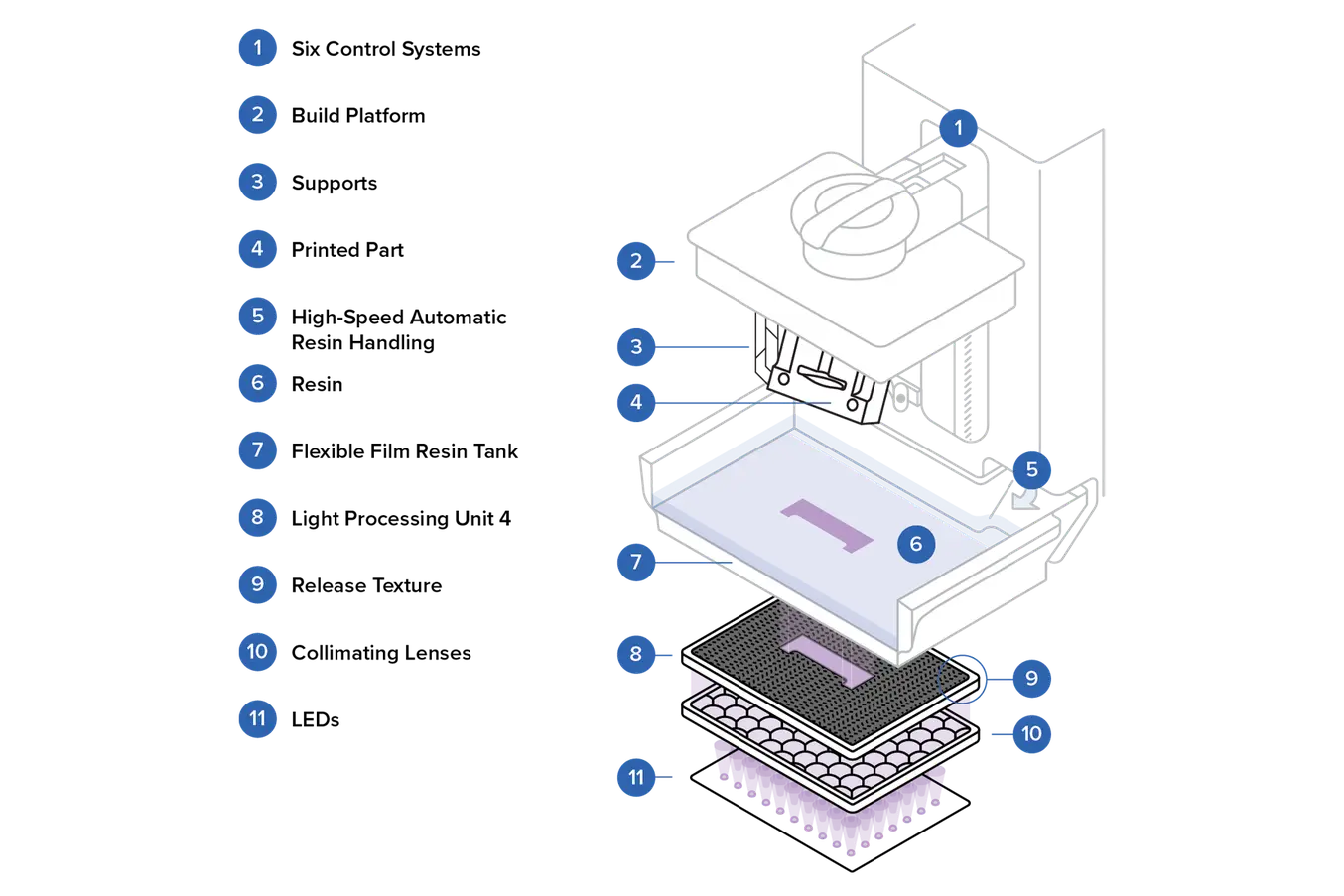
MSLA 3D Printing Technology: The video is taken from Formlabs
How They Work
SLA (Stereolithography): SLA uses a laser as the light source. The laser traces each layer point by point, curing the resin selectively. This process is highly precise but slower because the laser must individually draw every feature of the layer.
MSLA (Masked Stereolithography): MSLA employs an ultraviolet (UV) LED array combined with an LCD screen that acts as a mask. The LCD selectively allows light to pass through, curing an entire layer at once. This makes MSLA faster than SLA, especially for larger models or multiple parts printed simultaneously.
SLA 3D Printing Technology: The video is taken from Formlabs
MSLA 3D Printing Technology: The video is taken from Formlabs
Key Differences
Feature |
SLA |
MSLA |
Light Source |
Laser |
UV LED array + LCD mask |
Curing Method |
Point-by-point |
Entire layer simultaneously |
Speed |
Slower (laser traces each detail) |
Faster (layer-based curing) |
Precision |
Higher precision due to laser control |
Slightly less precise but still excellent |
Surface Finish |
Superior surface finish |
Excellent but may vary based on LCD resolution |
Cost |
Typically, higher due to laser system |
More affordable for consumer-grade printers |
Durability |
Long-lasting components |
LCD screens may require more frequent replacement |
Detailed Comparison
- Light-Curing Process:
- SLA uses a laser beam that moves across the resin tank to cure the resin layer by layer. This makes it slower but allows for extremely fine detail.
- MSLA employs an LCD screen to mask UV light, curing an entire layer at once. This significantly speeds up the process, especially for larger or batch prints.
- Speed:
- SLA is slower because the laser must trace each point individually.
- MSLA is faster since it cures entire layers simultaneously, making it particularly efficient when printing multiple objects on the same build plate.
- Precision and Detail:
- SLA offers slightly better precision due to the focused laser beam, making it ideal for highly intricate designs.
- MSLA still provides high resolution but may not match SLA’s detail in some cases.
- Cost and Accessibility:
- SLA printers are more expensive due to their complex laser systems.
- MSLA printers are more cost-effective and widely available for consumer use.
- Applications:
- SLA is preferred in industries requiring extreme accuracy, such as engineering or healthcare.
- MSLA is preffered for faster production and cost efficiency, making it popular among hobbyists and professionals alike.
Advantages of SLA
- High Precision and Detail: SLA excels in producing intricate designs with superior accuracy, making it ideal for industries like jewellery, dentistry, and engineering where fine details are critical.
- Smooth Surface Finish: The laser curing process ensures exceptional surface quality, reducing post-processing needs.
- Material Versatility: SLA supports a wide range of resins tailored for specific applications, such as biocompatible or heat-resistant materials.
Advantages of MSLA
- Faster Printing: By curing entire layers at once, MSLA significantly reduces print times, especially for larger models or batch production.
- Cost-Effectiveness: MSLA printers are more affordable and accessible for hobbyists and small businesses.
- Scalability: With its speed advantage, MSLA is well-suited for high-throughput production environments like dental labs or prototyping facilities.
Applications
SLA:
- Prototyping complex designs requiring high detail.
- Engineering, Automobile and Aerospace.
- Medical devices and dental appliances.
- End-use parts needing isotropic mechanical properties.
MSLA:
- Rapid prototyping with tight deadlines.
- Engineering, Automobile and Aerospace.
- Consumer-grade applications like miniatures or figurines.
- Batch production of similar parts with consistent quality.
Formlabs Innovations in SLA and MSLA
Formlabs has been at the forefront of advancing both SLA and MSLA technologies:
- The Formlabs Form 3+ series uses Low Force Stereolithography (LFS), an advanced form of SLA that improves surface quality and reduces print failures by minimizing peel forces during printing.
- The Formlabs Form 4 series introduce advanced MSLA technology with features like high-speed automated resin handling and durable Light Processing Units (LPUs), enabling faster print speeds and higher reliability compared to generic MSLA printers.
Choosing Between SLA and MSLA
The choice between SLA and MSLA depends on your specific needs:
- Choose SLA for precision, surface finish, and material versatility are your top priorities while 3D Printing.
- Choose MSLA for precise, rapid, versatile, cost-efficiency and surface finish 3D Printing.
For professionals seeking innovative solutions, Formlabs offers industry-leading SLA and MSLA printers designed to meet diverse requirements across industries.
By understanding these differences, you can select the right technology for your projects—whether it’s achieving unmatched detail with SLA or leveraging the speed and efficiency of MSLA.