Zortrax Endureal
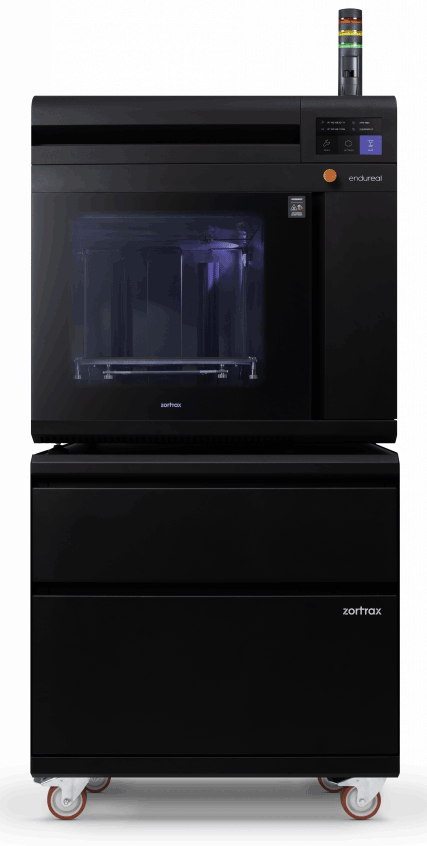
Industrial 3D Printer for high-tech manufacturing
Advanced thermal management enabling efficient work with high-performance polymers is what Zortrax Endureal 3D printer is all about. Temperature of filaments in Zortrax Endureal LPD Plus 3D printer is tightly controlled at each stage of processing to achieve utmost precision and best possible mechanical properties of 3D printed parts.
- High-temperature extruder: An advanced extruder can work at sustained temperatures as high as 480 °C to support processing demanding filaments.
- Heated printing chamber: Temperature in the printing chamber can reach up to 200 °C to ensure best thermal conditions for high-temperature materials.
- Heated build-platform: A build-platform supporting temperatures of up to 220 °C to ensure appropriate stability to models.
- Advanced thermal shielding: Thermally shielded extruder’s compartment is always kept at low temperatures to ensure uninterrupted filament transmission.
- Heated filaments’ compartment: Filaments are stored in a secure, closed environment at temperature optimal for both high performance and standard polymers the Endureal is designed to work with.
Why Zortrax Endureal Is Special?
Zortrax Endureal supports the high tech industrial materials like Z-Peek, BASF Ultrafuse® PPSU and Z-PIE 1010 which make Zortrax Endureal special among other FDM 3D Printers. Wide range of materials supported by Zortrax Endureal makes it possible to go from early low-cost prototypes to the final high-performing part using one manufacturing device.
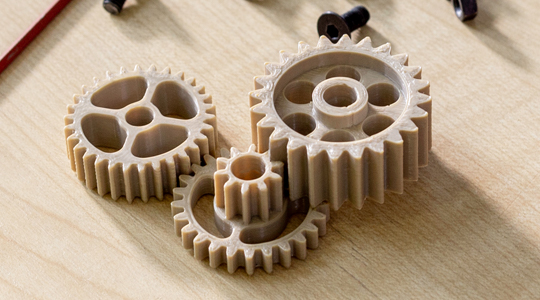
Z-Peek
Z-PEEK space-grade outgassing-compliant filament. Z-PEEK is one of the strongest polymers on the planet. It has strength-to-weight ratio comparable to stainless steel and the thermal properties suitable for exposure to low Earth orbit environment. Z-PEEK meets ESA’s outgassing requirements specified in standard.

Z-PIE 1010
Z-PEI 1010 robust thermally stable industrial material. Z-PEI 1010 belongs to the family of polyetherimides with higher rigidity, higher heat deflection temperature, and broader chemical resistance. This filament is aimed at chemical industry, automotive, aerospace, engineering and mass manufacturing scenarios.
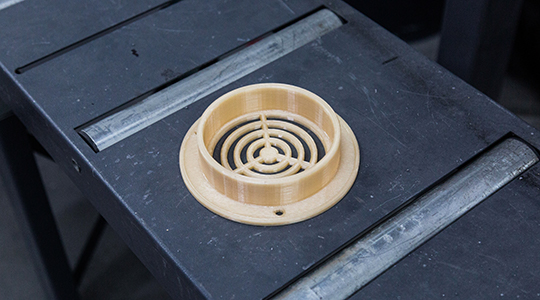
BASF Ultrafuse® PPSU
BASF Ultrafuse® PPSU is Flame-retardant industrial polymer with railroad certification. BASF Ultrafuse® PPSU is a polyphenylsulfone based 3D printing filament. One of its most important characteristics is fire resistance. It is designed by BASF specifically for 3D printing in aerospace and railroad applications.
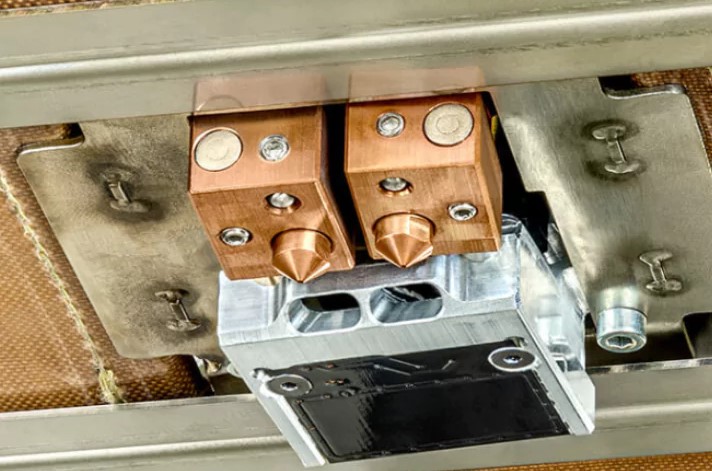
Dual-extrusion
Zortrax Endureal has a dual-extrusion system that can print high-temperature filaments with soluble support structures. Endureal is designed to process difficult materials. Both single and dual-extrusion modes are supported by the Printer.
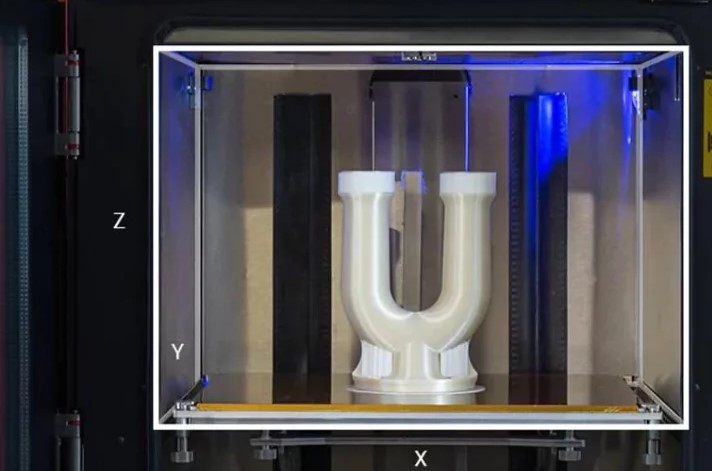
Large Build Volume
Build volume measuring 400 x 300 x 300 mm is large enough to accommodate full-sized structural industrial components. Due to soluble support printing capability, most of build volume can be used by stacking models in batches arranged on top of the other.
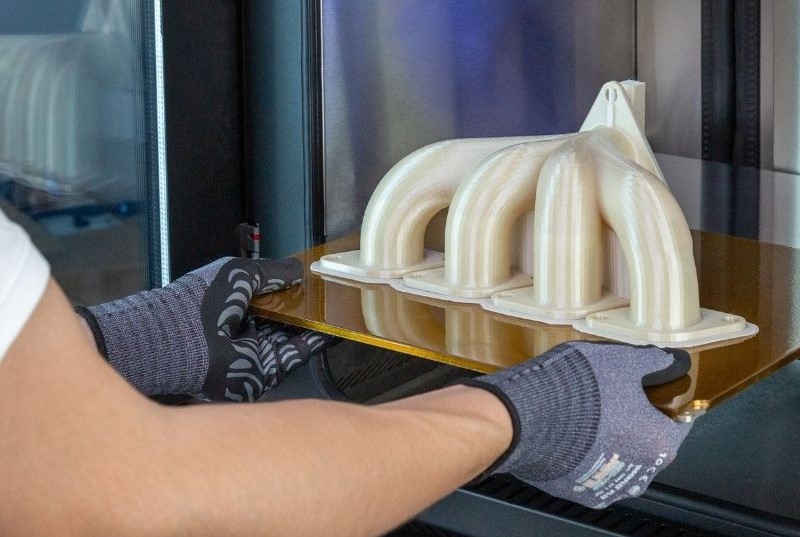
Aluminum build platform
Endureal has an aluminum build platform that can reach temperatures high enough to process high-performance polymers. To ensure proper adhesion of all filaments, a build plate made of ferritic steel covered with a PEI film is attached to the build platform.
Industrial safety systems
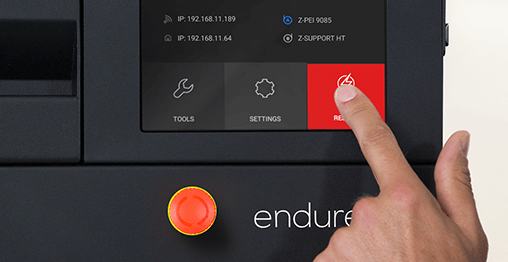
Black out response system
When a power outage is detected, Endureal uses the energy stored in built-in capacitors to save the exact position of the printing head. This way printing can be resumed from the same spot when the power is back on.
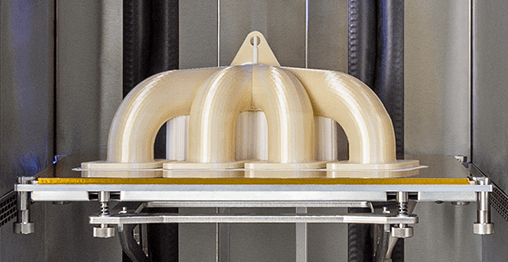
Monitored printing progress
Printing progress can be monitored remotely with a heat-resistant camera installed in the Zortrax Endureal printing chamber. The camera is capable of live video streaming and designed to work in demanding conditions.
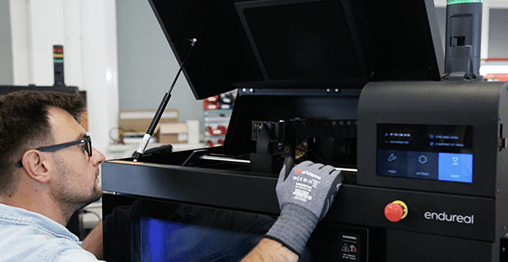
Advanced filament sensors
Separate sensors work at all times to detect events when filament is jammed or depleted. The printer also monitors the weight of the filament spools to determine if there is enough material to complete the printing process.
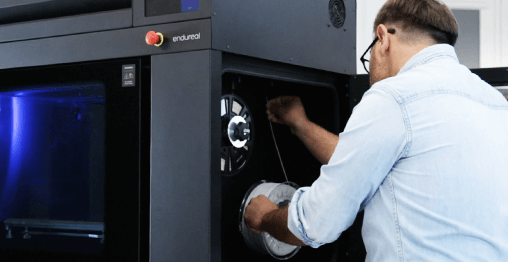
Controlled filament's compartment
Filaments’ compartment creates an optimal environment for storing material spools. It is equipped with a moisture absorber which is responsible for reducing humidity to levels appropriate for hygroscopic materials.
Specifications
Device
Build volume | 400x 300 x 300 mm (15.7 x 11.8 x 11.8 in) |
---|---|
Nozzle diameter | 0.4 mm (0.016 in) |
Extruder | Dual material |
Extruder cooling system | Two fans cooling the extruder, radial fan cooling the print |
Hotend | High Temperature dual hotend |
Platform | Heated; aluminium plate coated with PEI |
Material Endstop | 2 x mechanical endstop, 2 x material weight sensor |
Connectivity | Wi-Fi, Ethernet, USB |
Operating system | Android |
Processor | Quad Core |
Touchscreen | 7″ IPS 1024 x 600 |
Camera | Yes |
Temperature
Maximum printing temperature (extruder) | 480 °C (896 °F) |
---|---|
Maximum platform temperature | 220 °C (428 °F) |
Maximum build chamber temperature | 200 °C (392 °F) |
Ambient operation temperature | 17-30 °C (63-86 °F) |
Storage temperature | 0-35 °C (32-95 °F) |
Software
Software bundle | Z-SUITE |
---|---|
Supported file types | .stl, .obj, .dxf, .3mf, .ply |
Supported operating systems | Mac OS Catalina and newer versions / Windows 10 and newer versions |
Printing
Technology | LPD Plus (Layer Plastic Deposition Plus) advanced technology depositing melted thermoplastics with break-away and dissolvable support structures |
---|---|
Layer resolution | 200-250 microns (for 0.4 mm nozzle) |
Minimal wall thickness | 450 microns (for 0.4 mm nozzle) |
Platform leveling | Automatic measurement of platform points’ height |
Electrical
AC input | 120 V ~ 13 A 50/60 Hz 200 – 240 V ~ 9.5 A 50/60 Hz |
---|---|
Maximum power consumption | 120 V – 1600 W 200-240 V – 2300 W |